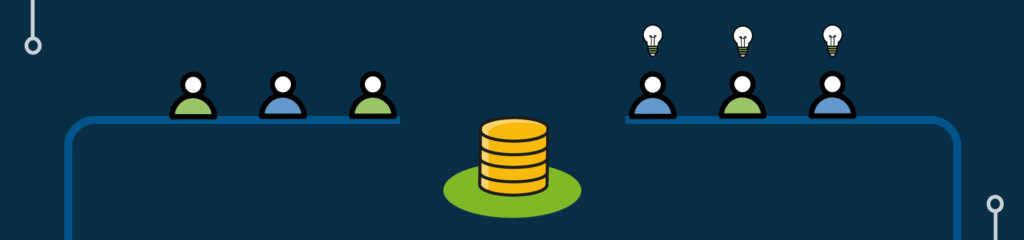
Share:
How manufacturers can bridge the skills gap with funding
The continuing issue of how to bridge the skills gap to attract and retain the best talent remains one of the most crucial to address. We explore how alternative finance may help to address the issue.
Among many issues facing manufacturers today – rising energy and fuel costs, the green transition, supply chain disruptions, inflation climbing at an exceptional rate, and post-Brexit rule changes to name only a few – the continuing issue of how to bridge the skills gap to attract and retain the best talent remains one of the most crucial to address.
A recent 2022 Make UK/PwC Senior Executive Survey showed almost 90 percent of firms were concerned about losing advanced skills, not only from their own business but from the entire manufacturing sector. More than two thirds of those questioned identified up-skilling younger staff and retaining experienced staff as their top priority, with almost half planning to invest in apprenticeships and job security measures.
Despite the UK remaining the ninth largest manufacturing nation in the world, reports suggested that British manufacturers face the largest shortage of skilled workers since 1989, caused by ongoing factors including:
- Experienced staff retiring faster than younger people entering the sector
- Outdated perceptions of the industry causing it to not rank highly compared to other career options and sectors
- The focus on gaining university degrees after leaving school
- A male-dominated workforce
- Digital and technological advances creating gaps in highly technical knowledge
These skill gap issues are partly hindering the growth of productivity in UK manufacturing, and with key advancements developing at exponential rates, such as the adoption of Industry 5.0, these issues need tackling as soon as possible else risk further damaging consequences to businesses and the sector as a whole. Without plans and steps to close the gaps, businesses will soon see:
- Diminishing institutional knowledge lost with the retiring aging workforce
- Decreased returns as businesses struggle to keep up with demand
- Stunted growth as less new opportunities and contracts arise
- Dissatisfied workforces that will leave to find better at competitor businesses
Addressing the skills gap
One key strategy to address issues and sustain the growth of the sector for the long-term is funding – with an array of flexible options to suit the needs of all UK manufacturing SMEs.
There isn’t one route that suits all when it comes to assessing the right funding options, but the first port of call should always be for decision makers to map out the skills gap relating to their business and see if traditional bank funders are available and suitable for the business’ need.
Investing in current workforces, training and seizing opportunities to build the business will attract and retain staff for a longer-term. Funding can be used for a multitude of business plans and help to attract talent and advisors.
Using investment to explore apprenticeships and trainee programmes is a good way to attract younger people to the sector and teach them that manufacturing isn’t still operating in the dark ages – with new technological advances, Industry 5.0 right around the corner and the digitalisation of working, having opportunities for people to learn while being employed allows business owners to shape workforces to match their business’ current processes and systems as well as having them learn about the new advancements that could be used within the company.
Investing to safeguard existing jobs allows the diverse expertise of key staff members to remain in the business. Retaining and securing these people allows them time to pass on and train younger and less experienced staff before retiring and taking their value added knowledge with them.
Using funding to adopt new technologies and leading trends such as digitalisation and Industry 5.0 will enhance the competitiveness of a business, not only by improving production efficiency but making working life better for employees and attracting prospects with enhanced skill sets.
But what to do when traditional bank lending is not an option nor appropriate?
The alternative funding landscape has grown exponentially with a plethora of lending products that can suits most business needs, such as those specialist funds provided by FDC.
Though it can be time-consuming for key decision makers to consider the wide array of options, taking the time to research and talk to trusted finance advisors who know their way round the full funding landscape can be a way of successfully securing funding to alleviate some of the stresses.
As well as providing finance, business owners often develop long-lasting relationships with alternative providers who are often able to share extensive talent pools and insights, adding value beyond just the money they provide.
FDC manufacturing investment
FDC is an alternative funder whose team has a wealth of knowledge and experience investing in the manufacturing sector. It manages the recycled Advanced Manufacturing Supply Chain Initiative (recycled AMSCI) that can be used to invest in training, job security and improve supply chain competitiveness. With loans from £500,000, the recycled AMSCI is targeted at SMEs in the manufacturing supply chain, including suppliers and innovators.
Andy Green, AMSCI Investment Director comments: “FDC aims to provide SMEs within the advanced manufacturing sector with the backing needed to continue to grow, build on success and expand their long-term capabilities.
“The recycled AMSCI fund in particular has been developed to address market failures, increase business capabilities and competitiveness as well as support job creation.
“More information about any of our funds can be found on our website and we encourage any decision makers looking long-term flexible funding for business growth to get in touch.”